符合市場需求的玻璃瓶制造程序
玻璃瓶生產過程中,會產生各種的缺陷產品,給產品帶來嚴重隱患。為了提高玻璃瓶出廠質量,玻璃瓶廠家現在靠人工檢查挑除廢品。但人工檢查速度慢,需要占用大量的人力、物力資源和場地資源,而且人眼極易出現疲勞和疏忽的情況。隨著計算機技術不斷發展,現在已經逐步使用計算機代替人工進行質量檢測,這樣檢測標準可以通過系統進行設置,不受主觀因素的影響,連續準確可靠地完成檢測工作。
玻璃瓶質量檢測要求
本系統針對藥用玻璃瓶的缺陷檢測,包括白色瓶、棕色瓶及有刻度的玻璃瓶等,如圖1所示。
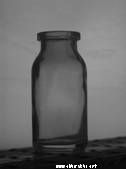
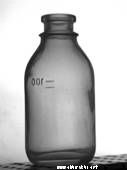
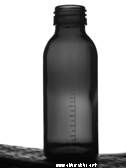
圖1 待檢測玻璃瓶示例
系統主要檢測功能包括:
A、尺寸檢測(包括玻璃瓶瓶高、玻璃瓶身外徑、玻璃瓶口外徑、玻璃瓶口高度等);
B\玻璃瓶身外觀缺陷(包括氣泡、雜質、褶皺、橫豎條紋、粘連、結石、裂紋、刻痕、擦傷及明顯的油臟、手印等);
C、玻璃瓶底缺陷從側面可以拍攝到(包括瓶底凹凸不平、底刺、偏底等);
D、玻璃瓶肩部缺陷(包括斜肩、歪瓶、與瓶身類似的外觀缺陷等);
E、玻璃瓶口部分的檢測內容是除了檢測玻璃瓶瓶身外觀上那些缺陷類型外,還需要檢測缺口、破口、圓口不齊等缺陷。
硬件設計
根據檢測缺陷類型的需求,系統采用五臺高速攝像機,當玻璃瓶在傳送帶上的運動過程中,系統采用外觸發方式在固定位置準確抓拍四個側面的圖像和一個玻璃瓶口圖像,然后圖像傳輸到兩臺高性能處理器中進行處理和分析計算,其結果匯總到一臺服務器上進行統一控制和顯示。攝像機選用大恒DH-HV1310FM,分辨率為1280*1024,支持8bit或12bit輸出。四個側面攝像機之間的夾角為90度,保證整個瓶的檢測沒有盲區。玻璃瓶口部分單獨采用一個相機進行處理,采用碗形燈光源進行拍攝圖像。
根據缺陷的特征綜合分析,發現對于玻璃瓶身外側缺陷,采用高亮度背光源的打光方式能很好地反映各種缺陷;對于玻璃瓶口表面缺陷,考慮生產線特點和充分反映玻璃瓶口表面缺陷的要求,自行設計一種碗形光源,這樣在不改變現有生產線設備上很好地檢測玻璃瓶口部分缺陷。
由于生產線上玻璃玻璃瓶的類型可能會根據需求經常更換(玻璃瓶高度范圍在15-150mm),鏡頭的選擇我們充分考慮這個因素,采用的是computar公司的M3Z1228C-MP變焦鏡頭,在本系統中獲得較好的圖像,同時滿足不同尺寸的玻璃瓶在視場內成像要求。
同時設計一個專用的信號處理器,接收處理傳感器的觸發信號,同時將觸發信號轉發到攝像機。另外可由接收圖像處理器發送來的剔廢信息,通過編碼器自動計算延遲行數并準確輸出剔廢觸發信號。
硬件整體結構如圖2所示:
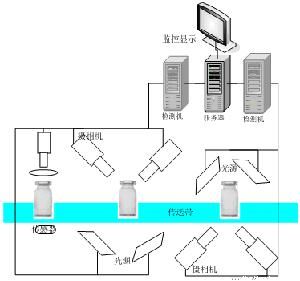
圖2 硬件系統結構原理圖
軟件設計
整個系統軟件采用VC++6.0開發,分為兩個部分:服務器部分完成信息的綜合,數據存儲以及后續的檢測結果信息統計分析;檢測端部分主要完成圖像采集和缺陷分析。對于檢測系統來說,其核心部分為缺陷檢測算法部分,系統算法部分是基于DHImage庫的基礎上自行開發完成,檢測算法流程如圖3所示。
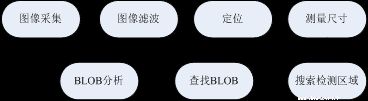
圖3 檢測算法流程圖
由于在生產線中輸送玻璃的傳送帶有時會發生抖動,導致拍攝的玻璃瓶圖像發生傾斜,為了精確地測量相關尺寸,我們必須對玻璃瓶進行定位。系統首先查找玻璃瓶外輪廓,然后采用基于輪廓配準的方法來精確定位,這為后續尺寸測量提供很好地保證。為了減少圖像邊緣很多陰影干擾,同時獲得盡可能大的檢測區域,我們在分析缺陷前增加了一個搜索檢測區域的步驟,主要就是根據玻璃瓶自身特點自動計算內部實際區域,同時對于一些在邊緣的缺陷(氣泡,裂紋)進行預判。在后面的BLOB(連通區域塊,可能是缺陷或是干擾)分析中,我們充分考慮玻璃瓶掛霜不均勻性,玻璃瓶厚度不均勻性等的影響,并對薄皮、炸身等不明顯缺陷特征進行深入分析,其中部分缺陷圖像示例如圖4所示,開發一套專門針對玻璃瓶缺陷分析的算法模塊。
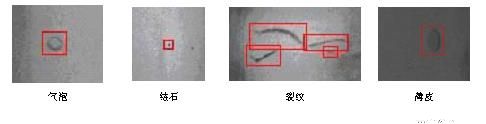
圖4 部分缺陷圖像
現場測試結果
在系統開發階段,我們在實驗室采用與現場類似的傳送帶和輸瓶機等機械設備,設計安裝一套玻璃瓶自動輸送系統,通過在實驗室連續一個月的系統測試后,我們把這套系統分階段地安裝在白色瓶、白色帶刻度瓶、棕色瓶、棕色帶刻度瓶以及管瓶生產線,其系統主監控界面如圖5所示。
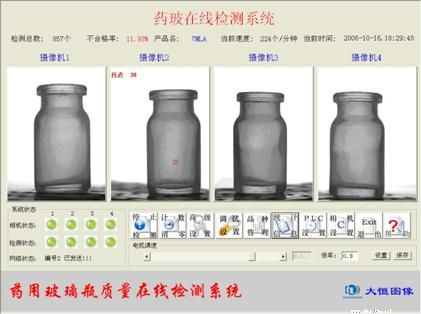
圖5系統運行主界面
在實際使用中我們根據各種不同種類玻璃瓶特點,完善檢測算法,最后進行優化整合,現在檢測系統根據選擇不同選項,靈活地根據生產需要檢測不同種類的玻璃瓶。
通過一年多現場使用表明,該系統完全能滿足藥用玻璃瓶質量檢測要求,大大提高其生產效率,同時為生產合格的產品提供有效保證。但為了提供完美的檢測設備,我們在保證現有檢測速度的同時需要在以下幾個方面繼續研究:對于瓶口有螺紋部分缺陷的研究;對于不規則刻度部分缺陷的研究;對于瓶底部分小缺陷研究;完善對缺陷玻璃瓶的錯誤類型統計分析,為工廠改進生產工藝提供參考